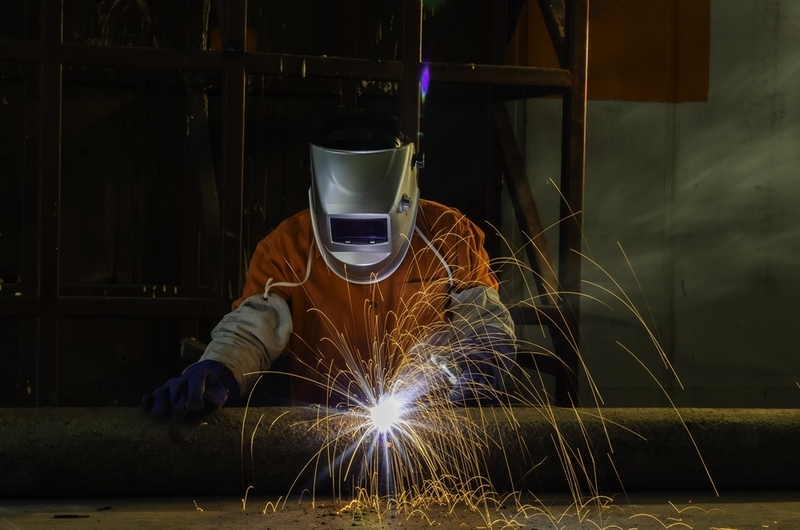
용접(Welding)은 서로 다른 두 개의 금속 및 비금속 를 접합해 새로운 가치를 부여하는 공정이다. 별도의 용가재를 열로 녹여 소재를 잇는 ‘경납땜(Brazing)’이 용접의 기원으로 알려진다. 이어 방전 현상을 이용해 아크열을 발생시켜 용가재를 용융해 소재를 용접하는 용접 공법인 이른바 ‘아크 용접(Arc Welding)’, 아크 용접에서 소모성 용가제를 활용한 가스메탈아크용접(Gas Metal Arc Welding)’ 등이 근현대를 대표하는 용접 방식이다.
이때 기본적으로 금속 소재가 용접 공정에 주로 활용되지만, 기술이 발전하면서 플라스틱·세라믹 등 국내 뿌리기술 소재를 접합하는 용접 공법들도 줄곧 탄생하고 있다. 이러한 용접 공정은 전 세계 산업의 근간으로, 별도의 부자재를 활용해 물체를 잇는 타공정 대비 견고하면서도 흔적이 남지 않는 등 효율적인 접합 방식으로 지금까지 활약하고 있다.
우리나라는 ‘뿌리산업 진흥과 첨단화에 관한 법률’ 제1조에 6대 뿌리기술 중 하나로 용접을 선정해 주요 기술로 인정하고 있다. 용접 기술은 현재 자동차, 전기전자, 조선, 건설, 기계, 항공우주, 로봇, 원자력, 중공업 등 국내 전통·유망·차세대 산업을 잇는 기반으로 자리잡았다.
특히 자동차 업계는 전기자동차(EV)를 미래 먹거리로 구상하며 전환기를 맞이한 만큼 품질의 종착지로 평가받는 ‘용접 기술’의 고도화를 노리고 있다. EV는 경량화·효율성·친환경성을 필두로 지속 성장하는 분야이기 때문에 차세대 용접 기술이 요구된다.
기존 자동차 용접 공정은 ‘저항 점 용접(Resistance Spot Welding 이하 RSW)’을 주요 공법으로 채택한다. RSW는 압력과 열을 동시에 이용하는 방식으로, 금속 기반 판재를 서로 가압해 접촉 후 전류를 통전 시켜 금속 판재 계면을 용융 후 접합한다.
이때 용접 품질을 확인하는 방식은 파괴 검사(Destructive Testing)와 비파괴 검사(Non Destructive Testing)로 구분된다. 이 중 파괴 검사는 접합부의 계면을 파괴·해제해 검사를 수행하기 때문에 신뢰성은 확보되지만 비용·시간 등 자원이 수반된다는 단점이 있다. 또 일부 용접부를 파괴해 대략적인 품질을 검사하는 샘플링 방식이 있지만 이 또한 용접 부분을 해체해야 하기 때문에 이 또한 명확한 한계를 드러낸다.
반면 비파괴 검사는 용접부를 분해하지 않고 검사를 수행하는 형태로, 지금까지 초음파 기반 기술을 많이 활용했다. 작업자가 수작업으로 모든 저항 점용접 구간을 수동 접촉하는 방식으로 진행된다. 또 초음파 스캔을 통해 도출된 데이터는 용접부의 표면 특성 및 측정 엔지니어의 숙련도에 따라 정확도·신뢰성 또한 100%에 다다르기 어렵다는 단점이 있다. 사람을 로봇으로 대체하는 자동화 요소를 이식하는 사례가 늘어났지만, 여전히 측정 속도 및 용접점 위치 정확도 측면을 충족하지 못했다.
그렇다면 앞선 한계를 극복하는 자동차 접합 품질검사를 수행하기 위해서는 어떤 기술이 필요할까?
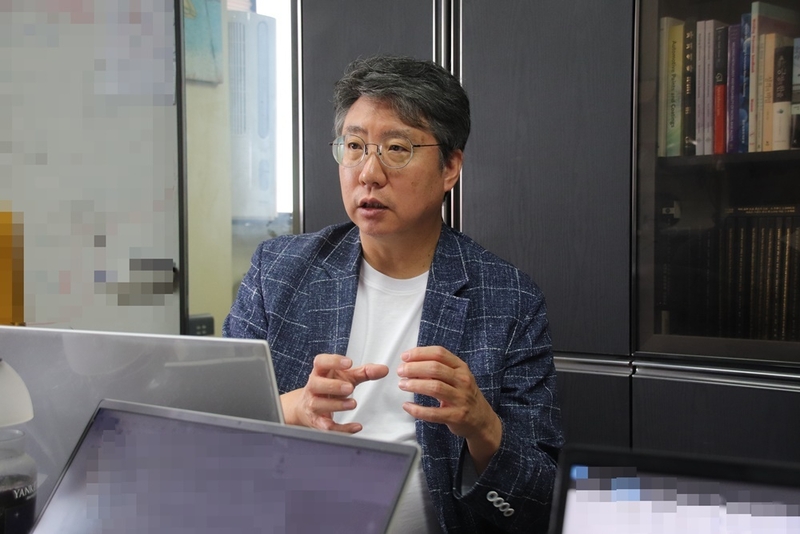
용접 품질의 신기원 제시하다...3D 스캐닝 품질관리 시스템이 차세대 스타
박영도 동의대학교 신소재공학과 교수 겸 대한용접·접합학회 국제 부회장은 머신비전 카메라와 3D 스캐닝 기술을 강조한다. 박 교수는 품질검사 자동화에 기여할 핵심 요소로 양 기술을 내세웠다.
두 방식 중 머신비전 카메라 기술은 육안으로 확인할 수 있는 용접 표면을 검사하는 데 활용된다. 대상물 내부 접합 상태 파악은 3D 스캐닝 기술이 담당한다. 기존 초음파 기술에서 한 차원 진화된 형태로 주목받고 있다. 박영도 교수는 RSW 공정 중 접합부에 발생하는 ‘너겟(Nugget)’과 용접 과정에서 표면에 찍히는 ‘압흔 포인트’에 주목한다.
박 교수는 “3D 스캐닝 방식 기반 용접 품질검사는 내부 너겟 직경 파악이 핵심”이라며 “이는 표면 압흔 크기 및 형태가 내부 너겟의 크기를 파악할 수 있는 지표이기 때문에 압흔을 정밀하게 측정하는 기술이 필수”라고 설명했다. 이 과정에서 세밀한 표면 압흔 형상 데이터를 얻기 위해 높은 해상도의 점군 데이터가 필요하다.
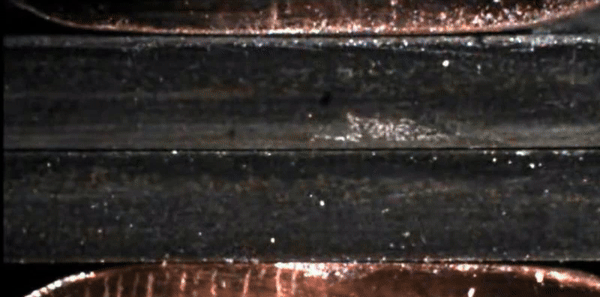
압흔 모양새가 용접 외부 퀄리티 결정..."내부 너겟 품질 파악까지 이어져"
국내 자동차 OEM과 협력해 관련 연구를 진행한 박영도 교수팀은 이때 레이저 기반 3D 스캐닝 기술을 적용해야 함을 인지했다. 이 과정에서 모재 강도·두께, 패널 겹 수 및 적층 순서, 압흔부 내부 결함 및 오염 정도 등 압흔 데이터에 영향을 미치는 변수를 최소화하기로 했다. 이는 압흔 크기 및 형상과 너겟 간 상관관계를 명확히 하는 데 핵심적인 요소다.
교수팀은 압흔 데이터의 변수를 차단하기 위해 ‘그래프 합성곱 신경망(Graph Convolutional Neural Network, GCNN)’ 기반 머신러닝 기법을 활용했다. GCNN은 객체 간 관계를 명확히 정립하는 기술로, 이를 머신러닝에 활용함으로써 각종 압흔 데이터를 분석·정립하는 룰 베이스 알고리즘(Rule Based Algorithm) 개발이 가능했다.
박영도 교수팀은 이를 고도화해 용접 품질검사를 통합한 최적화 알고리즘을 결과로 내놨다. 이 기술은 점 용접부 외관 결함 분류 검사와 너겟 직경 예측 등 두 가지 프로세스를 수행한다. 외관 결함 분류 검사 과정에서 앞선 GCNN 기반 머신러닝 기법으로 획득한 압흔 데이터를 통해 용접부 표면 결함을 확인한다.
이 과정에서 3차원 좌표 데이터인 ‘포인트크라우드(Point Cloud)’와 매쉬폴리건(Polygon) 형태의 ‘STL(Stereo Lithography)’ 파일 등을 활용해 외부 용접점의 품질을 검사한다. 박 교수는 이때 차체(Body In White) 한 대를 측정할 경우 활용되는 스폿 용접 데이터는 총 4000개 이상이라고 강조했다.
교수팀은 이를 통해 ‘정상’, ‘가장자리 용접(Edge Welding)’, ‘틸팅(Tilting)’, 표면 날림 이른바 ‘쇠가시’, 내부 기공이 표면으로 돌출 된 ‘핀 홀(Pin Hole)’, ‘전극 마모’ 등으로 구성된 압흔 형상 결함 데이터를 도출했다.
이렇게 표면 압흔 모양새를 확인했으니, 궁극적 목적인 너겟 성장을 확인해야 한다. 박 교수팀은 직경·면적 등 총 16개 항목으로 구성된 압흔 데이터를 차용해 너겟 직경을 예측했다. 압흔 데이터를 값을 추출한 후 인공신경망(Artificial Neural Network) 모델 기반 딥러닝 기법과 룰 베이스 알고리즘을 적용했다. 이때 20000개 이상의 판재 조합, 시편 겹 수 등 각종 표본이 활용됐다.
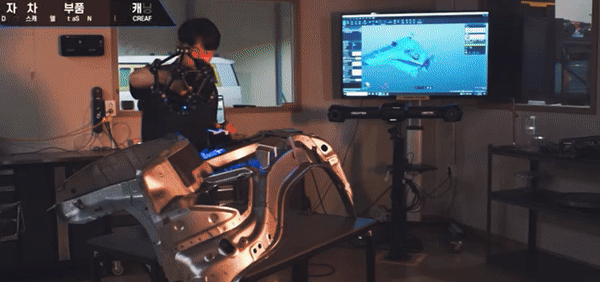
기술 융합 시대, 로봇도 시스템에 참전한다
앞선 연구를 통해 탄생한 3D 스캔 저항 점 용접 품질검사 시스템 ‘TESCar-RSW’는 해당 연구 프로세스 내 모든 과정을 구현하는 차세대 용접 품질검사 솔루션이다. 박영도 교수는 TESCar-RSW를 실제 자동차 생산 공정에 배치하기 위해 현장의 목소리를 경청했다.
함께 연구를 진행한 자동차 OEM과 논의 끝에 전체 검사 프로세스 사이클타임 100초 이내, 개별 점용접 당 검사 속도 1초 내외, 한 품목 사이클타임 내 보고서 출력 및 불량 용접점 산출 등 세 가지 요건을 충족해야 한다는 결론에 다다랐다.
박 교수는 먼저 용접부당 검사 속도를 충족하기 위해 차체 양쪽에 3D 스캐닝 로봇을 각각 배치한 레일을 설치하는 방식을 제안했다. 이와 동시에 3D 스캐닝 측정 영역을 그룹별로 세분화했다. 이는 검사·데이터 수집 등 차체 하나당 수행되는 프로세스 효율 극대화를 기대하게 한다. 여기서 로봇 스캐너는 국소적인 스캐닝이 아닌, 방대한 스폿 용접점 영역을 훑는 방식을 채택했다.
아울러 이를 통해 도출되는 리포트는 텍스트 및 그래픽 사용자 인터페이스(GUI) 기반으로 구성된다. 불량 포인트가 발생하면 디스플레이를 통해 타점이 빨간색으로 표시돼 작업자 입장에서 가시적인 분류가 가능하다.
박영도 교수는 “이번 연구 결과는 비파괴 기반 용접 품질검사 프로세스에 한 획을 그을 차별화된 시스템의 탄생을 알리는 것”이라며 “검사 및 판정 신뢰도를 지속 개선해 FDS(Flow Drill Screw), SPR(Self Piercing Rivet), REW(Resistance Element Welding) 등 기계식 접합 공정을 대상으로 한 도입 가능성을 타진할 것”이라고 포부를 밝혔다.
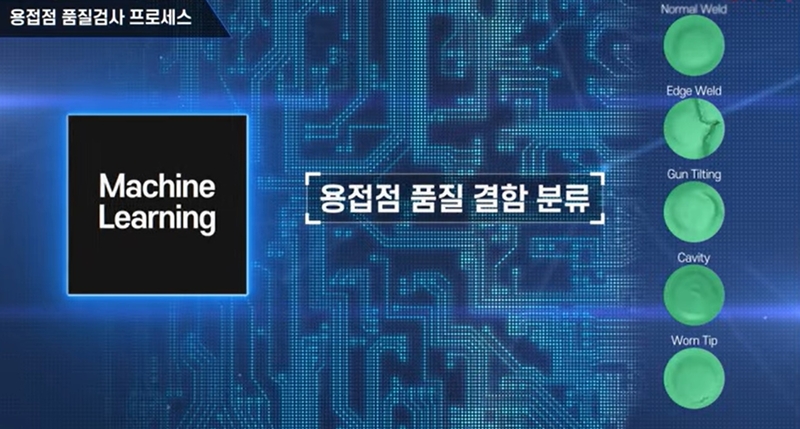
“용접 품질 영역의 완전한 스마트 팩토리 가능해...나아가 자율제조 실현에도 키 쥔다”
박영도 교수팀은 현재 3D 측정 솔루션 업체 ‘크레아폼’과 협력하고, 자동차 OEM 생산공장에 시스템을 도입해 개념증명(PoC)을 진행하고 있다. 박영도 교수가 점치는 용접 품질검사의 미래상은 어떨까?
Q. 기존 자동차 용접 품질검사는 어떻게 진행됐나?
A. 기존 비파괴 검사는 초음파로 내부 상태를 추측하고, 외부는 카메라 비전 시스템을 기반으로 시행되는 형태였다. 파괴 검사는 한 달 주기로 시제품 전체를 뜯어내 육안으로 확인하고 일일이 분석하는 표본 검사가 주를 이뤘다. 양 방식은 스마트 팩토리 체제는 적합하지 않다고 판단해 더욱 고도화된 방식을 고민하게 됐다.
Q. 전수검사는 ‘품질검사의 꽃’으로 평가받는다. 해당 기술은 전수검사에도 적용 가능한가?
A. 결론부터 말하면 가능하다. 통상 자동차에 녹여지는 용접점은 약 4000~5000개 수준이다. 이것을 기존 방식으로 검사하게 되면, 보고서 도출까지 최대 3일 이상의 시간이 소요되고 그에 따라 발생하는 비용도 상당하다.
대부분의 자동차 OEM은 당연하게도 품질 검사 과정보다 품질에 대한 결과가 정확하고 빠르게 도출되는 것을 선호한다. 또 비파괴 검사, 자체적 용접점 데이터 확보 등 요소를 고려하는 경향이 강하다. 우리 연구팀의 기술은 사이클타임 내에서 실시간으로 검사 결과를 도출하고, 데이터 관리도 수시로 가능하기 때문에 자동차 OEM 업계의 요구사항을 충족할 수 있다. 품질 검사에 이식되는 3D 스캐닝 기술이 더욱 강력해지려면 라이프 사이클 전반에 걸친 생태계의 협력이 필요하다.
Q. 현재는 자동차 산업에만 초점을 맞추고 있다.
A. 지금 이 시점에서, PoC 단계에 진입했기 때문에 자동차 업계를 위주로 도입 가능성을 추진하고 있다. 이 기술이 실제 자동차 생산 현장에서 증명되면, 자체 기술을 지속 개선할 계획이다. 이를 확장해 연구 규모를 더욱 확충하고, 이 기술이 배치되는 산업 영역을 한층 넓힐 생각이다. 향후 이차전지, 조선 등 한층 확장된 분야에서 이 기술이 활약하게 될 것이라고 생각한다.
헬로티 최재규 기자 |